All About Welding: Key Insights Into Techniques and Finest Practices for Success
Welding includes a range of techniques, each suited for particular materials and applications. Recognizing these approaches, such as GMAW, SMAW, and TIG, is vital for attaining ideal outcomes. The ideal equipment and safety practices can not be neglected. As preparation and repairing play crucial roles in the welding procedure, understanding these components can considerably improve the high quality of the last item. What are the vital elements that assure a successful weld?
Understanding Different Welding Methods
Welding techniques include a range of methods, each fit to particular applications and materials. Amongst the most common techniques are Gas Steel Arc Welding (GMAW), Secured Metal Arc Welding (SMAW), and Tungsten Inert Gas Welding (TIG) GMAW, also called MIG welding, is popular for its rate and versatility, making it optimal for thin materials. SMAW, or stick welding, is favored for its simplicity and performance in exterior settings, particularly with thicker metals. TIG welding uses precision and control, making it suitable for intricate work and non-ferrous metals (Belgrade Welding). Each technique has its unique benefits and factors to consider, allowing welders to pick the most effective method based on the job's needs, material kind, and desired end results. Understanding these techniques is essential for successful welding
Crucial Welding Tools and Tools
While different welding techniques require specific skills, the appropriate tools and tools are similarly important for achieving quality results. Crucial welding devices consists of welding equipments, which differ depending upon the method-- such as MIG, TIG, or stick welding. Protective gear, including headgears, aprons, and handwear covers, warranties safety and convenience throughout the procedure. Furthermore, clamps and components help secure materials in area, making sure accuracy in welds. Consumables like welding poles, cable, and shielding gas are also crucial parts that affect the high quality of the weld. Tools such as grinders and cutters help with surface prep work and post-weld completing, adding to an expert result. Investing in top quality equipment ultimately improves the performance and efficiency of welding tasks.
Security Practices in Welding
Proper safety and security methods are important in the welding industry to secure workers from potential risks. Welders should put on appropriate personal protective devices (PPE), consisting of headgears with correct shading, handwear covers, and flame-resistant garments. Sufficient ventilation is crucial to decrease exposure to hazardous fumes and gases generated throughout the welding procedure. In addition, employees ought to be learnt the appropriate handling of welding equipment to avoid mishaps. Fire safety and security measures, such as keeping flammable products away from the welding area and having fire extinguishers readily available, are required. Normal assessments of devices and workspaces can help identify prospective risks prior to they result in crashes. By sticking to these security practices, welders can create a safer working setting and reduce risks connected with their profession.
Preparing Materials for Welding
Preparing products for welding is an essential step that substantially influences the high quality and integrity of the final product (Montana Mobile Welding and Repair). Appropriate prep work includes cleaning the surface areas to remove pollutants such as dirt, rust, and oil, which can endanger the weld. Strategies such as grinding, fining sand, or making use of solvents are frequently employed to accomplish a tidy surface area. Additionally, guaranteeing that the products fit together well is necessary; gaps can lead to weak welds. It's also essential to consider the positioning and positioning of the elements, as this will certainly impact the convenience of welding and the final result. Selecting the ideal filler material and making certain compatibility with the base metals is important for accomplishing strong, resilient welds.
Tips for Getting High-Quality Welds
Attaining high-quality welds calls for attention to information and adherence to best practices throughout the welding process. Correct joint preparation is essential, making sure surface areas are clean and cost-free from contaminants. Selecting the proper filler material and welding strategy based upon the base metals is important for excellent bonding. Preserving regular traveling rate and angle while welding can prevent defects and advertise harmony. Additionally, regulating warm input is important; extreme heat can cause bending and damaged joints. Regularly inspecting the welds throughout the process permits instant adjustments if essential. Employing proper post-weld therapies, such as cleansing and tension relief, can improve the sturdiness and stability of the weld, ultimately guaranteeing a successful end result.
Troubleshooting Typical Welding Issues
Welding frequently presents obstacles that can affect the high quality and stability of the final item. Typical problems such as porosity, irregular weld grains, and overheating can emerge, each requiring particular fixing strategies. Comprehending these troubles is important for welders to improve their abilities and attain ideal outcomes.
Porosity Troubles Discussed
Porosity can often be forgotten, it remains an essential problem in welding that can compromise the stability of a finished product. Porosity describes the visibility of small gas pockets within the weld bead, which can deteriorate the joint and lead to early failing. This issue normally occurs from impurities, dampness, or inappropriate shielding gas coverage during the welding procedure. To mitigate porosity, welders should verify that the base materials are dry and tidy, use appropriate shielding gases, and keep regular welding criteria. Frequently inspecting the tools and atmosphere can likewise assist identify prospective concerns prior to they show up in the weld. Resolving porosity effectively is crucial for attaining strong, sturdy welds that fulfill top quality criteria.
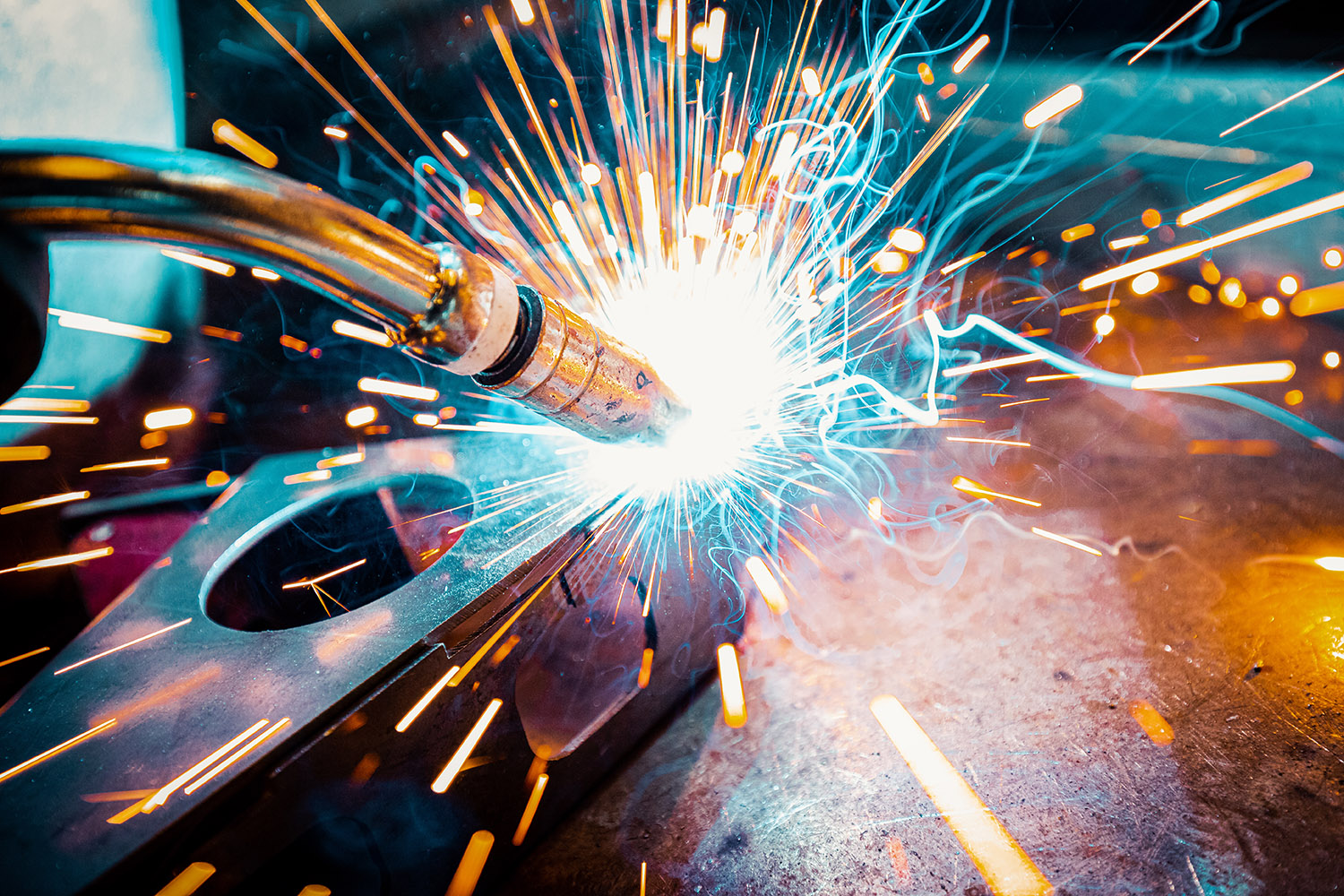
Irregular Weld Beads
Inconsistent weld beads can considerably affect the high quality and stamina of a completed usa weld item. Different elements important link add to this issue, including inappropriate traveling rate, wrong amperage setups, and inconsistent electrode angles. When the welder moves as well promptly, a grain may show up narrow and do not have infiltration, while moving as well gradually can cause too much buildup. Furthermore, making use of the wrong amperage can lead to either undercutting or excessive spatter, both of which compromise weld integrity. The welder's technique, such as inconsistent lantern motion, can also result in uneven grain appearance. To alleviate these problems, welders must concentrate on maintaining consistent, regulated movements and ensuring appropriate tools setups to achieve harmony in their welds. Consistency is key to attaining solid and reliable welds.
Getting Too Hot and Warping Issues
Extreme warm throughout the welding procedure can lead to significant overheating and contorting issues, affecting the structural stability of the workpiece. These problems typically materialize as distortion, which can compromise alignment and fit-up, making additional setting up testing. Variables contributing to overheating include the selection of welding criteria, such as voltage and travel rate, in addition to the kind of product being welded. To alleviate these concerns, welders need to maintain consistent travel speed and ideal heat input while keeping track of the work surface temperature. Additionally, preheating or post-weld warm treatment can aid minimize tensions triggered by quick cooling - Belgrade Fabrication. Routine examination and adherence to ideal practices are vital in preventing getting too hot and making certain the longevity and integrity of welded frameworks
Frequently Asked Questions
What Are the Occupation Opportunities in the Welding Sector?
The see this page welding industry provides diverse occupation possibilities, including positions as welders, teachers, examiners, and engineers. Specialists can operate in production, building, aerospace, and automotive industries, profiting from strong need and competitive salaries in numerous functions.
Exactly How Can I Improve My Welding Rate Without Giving Up Top Quality?
To boost welding speed without compromising top quality, one ought to exercise efficient techniques, preserve tools, enhance settings, and improve hand-eye sychronisation. Routine training and looking for feedback can also greatly add to accomplishing quicker, high-grade welds.
What Qualifications Are Readily Available for Welders?
Many certifications exist for welders, consisting of those from the American Welding Culture (AWS), the National Facility for Building Education and Study (NCCER), and different industry-specific organizations. These qualifications boost employability and show skill effectiveness.
Just How Does Welding Affect the Properties of Metals?
Welding affects the residential or commercial properties of metals by altering their microstructure, which can cause modifications in ductility, solidity, and toughness. Warm input and air conditioning rates throughout the procedure considerably impact these product attributes.
Can I Weld Dissimilar Metals Together?

Comments on “Why overheating affects welds and Montana Mobile Welding and Repair Welding’s approach to fix it”